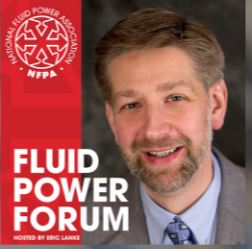
Volkmann Engineer Explains Pneumatic Vacuum Conveying on Podcast
Bill Fucich Reveals Reasons for Intense Demand
Our pneumatic vacuum conveying technology has developed quite a loyal following within powder and bulk processing circles over many decades and now it’s getting attention outside the process industries. More and more engineers want to know how to move products and materials of all kinds as fast, safely, and efficiently as possible and they see our approach as a novel way to automate a wide range of material handling tasks and solve staffing, maintenance, and other pressing issues. Eric Lanke, the host of the prestigious Fluid Power Forum podcast, for example, recently read an article about our conveyors and invited us to explain how pneumatic vacuum technology works, where it’s currently being used, and why engineers are taking a closer look at its potential applications.
Our own Bill Fucich, senior sales engineer, explained to Eric and his listeners that the rapidly growing awareness about our conveyors is due to its key advantages versus other ways to move material from one point to another. Bill cites the conveyor’s enclosed nature that protects ingredients like sugar and salt from contamination from exposure to the plant environment (and protects workers from exposure to dust); the explosion-proof design that allows safe installation in Class I and Class II hazardous environments; the ability to quickly disassemble the entire receiver with no tools for cleaning; and to work without any electricity or rotating parts.
Bill describes how the vacuum conveyor works in detail and how our vacuum pump uses the venturi principle to create enough suction via compressed air to transfer difficult materials with high bulk densities like copper and stainless steel as well as materials with very low bulk densities like fumed silica. Discussing key applications, Bill highlighted the role of our PowTReX conveying system in the growing additive manufacturing – 3D printing industry. The PowTReX conveyor transfers metal powders to 3D printers, then captures, screens, and returns the powdered metal to storage or to a hopper for reuse.
Bill also explained the differences between our Volkmann PPC Series conveyors for pharmaceutical and other hygienic applications and the Volkmann VS Series conveyors, which he calls “the workhorse” for transferring chemicals and almost anything else that doesn’t require cGMP compliance.
But it’s the engineering challenges that Bill calls the sweet spot of our operation – and we all agree that we’re at our most innovative when challenged with an application that nobody else wants to touch.
Listen to the podcast episode here.