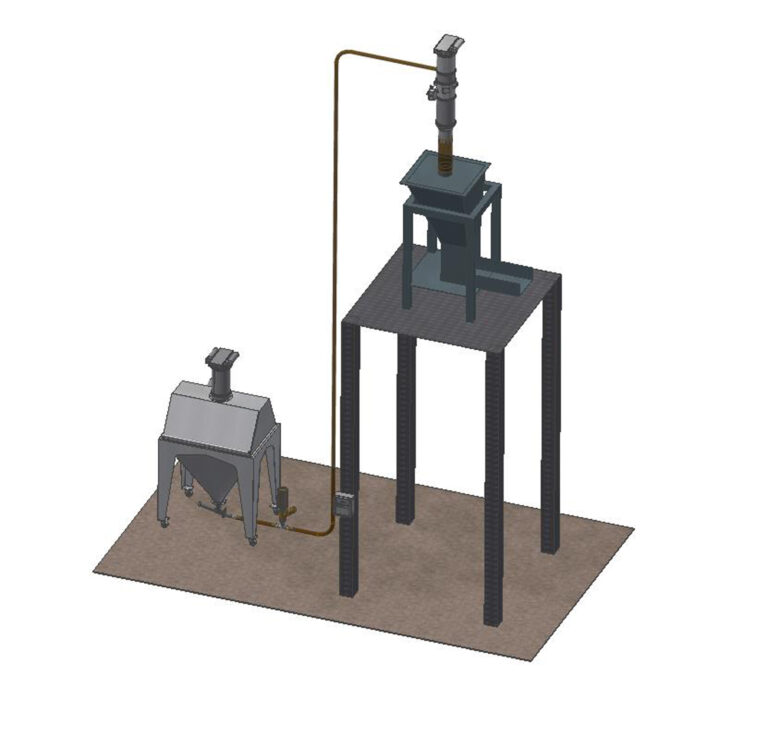
Up and In: Pneumatic Vacuum Conveying Automatically Loads Hoppers, Mixers, Tanks
What’s the most common bulk material transfer application across every industry? From a review of orders from customers who buy pneumatic vacuum conveying equipment, the most frequently cited application is the classic “up and in” installation. The up and in involves transferring powders and other bulk materials from floor level up and in to load or fill a hopper, feeder, tank, mixer, reactor, or other equipment. It’s so commonplace as an essential step in most industrial processes that it’s still often performed by hand and completely overlooked as an opportunity to cut costs, increase speed, and improve efficiency. In fact, the majority of our up and in vacuum conveyor customers need to transfer materials up and in two, three, or more times in the same process to move materials from production to filling and final packaging.
In many of these cases, Volkmann vacuum conveyors offer the ideal combination of capabilities for these applications:
- gentle material transfer
- the ability to go up steep and vertical inclines
- high throughput
- explosion-proof reliability by design
- sanitary compatibility
- versatility to transfer a wide range of different materials
In some other cases, it may be possible to use a bucket elevator, flexible screw conveyor, tubular drag conveyor, or even an open belt conveyor with success. But in every case, any of these automated conveying approaches offers a vast upgrade versus the cumbersome manual methods many companies still use to transfer and load their materials.
Manual Material Loading Breaks Bags, Breaks Backs
Most manufacturers who work with powders, pellets, and other dry solids began their operations doing nearly everything manually. They stacked 50-pound bags of salt, sugar, flour, lime, clay, or other materials in storage, carried them across the plant to the mixer, for example, and then emptied the big bags in a cloud of dust. Carrying these heavy bags up a ladder or up a flight of stairs to reach a port was just part of the job. The inherent risks of slips, trips, and falls, back injuries, product contamination, and dust explosions due to static electricity when handling powders by hand are inescapable.
Then, as growth demands scaling to larger volumes and higher throughputs, some manufacturers buy more bagged powders and hire more staff to fill bigger tanks and vessels. But the safety risks, systemic inefficiencies, and reliance on workers to show up and work every day grow, too. More savvy manufacturers, however, consider automating this material transfer process with vacuum conveyors, pneumatic conveyors, and other proven approaches that one worker can operate at the press of a button.
Instead of hauling big bags over the shoulder and up stairs to the discharge, a pneumatic vacuum transfer system automatically conveys the material from a silo, bulk bag unloader, sack tip station, drum or other container through flexible tubing or pipe up and into the discharge. No heavy lifting. No stairs or mezzanines. No dangerous vapors, splashing, or combustible dust clouds. This approach sets a vacuum pump at the discharge end inches above the hopper and gently draws the material through the tubing via negative pressure suction. Volkmann Multijector vacuum pumps create more than enough suction to allow for curves, vertical inclines, and long distance runs. This is the patented innovation that established Volkmann as the leading vacuum conveyor manufacturer.
It’s an enclosed system that protects the material from exposure to air, moisture, and contamination, and also protects workers from exposure to the material. For food, beverage, nutraceutical, and pharmaceutical products, such as for conveying candies, tablets, or powdered supplements to the packaging line, or for conveying hygroscopic products such as salt or silica gel, product containment and sanitation are critical. Open-air approaches such as belt conveyors and bucket elevators just won’t do.
Automated Material Loading Saves Time
Imagine one worker emptying a 50-pound bag of wheat flour into the hopper of our RNT sack dumping station at floor level. With the press of a button on the control panel, the powder conveyor automatically transfers the flour inside the flexible tubing 15 feet up a steep incline and then discharges it through a dust-tight connection into a weigh feeder hopper for mixing. When the hopper is empty, the conveyor stops automatically. Transferring up and in from a Gaylord or drum? One worker using our handy suction wand can completely empty a container in a few minutes.
Or, for transferring larger volumes from a bag unloading station, for example, just press the button. The vacuum conveyor empties the entire bulk bag and transfers it up and in to the hopper.
For more on how Volkmann pneumatic vacuum conveyors automatically transfer powders and dry, bulk solids, see details here.