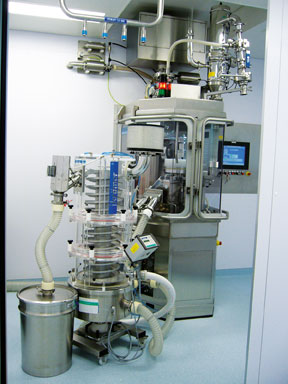
Growing Nutraceutical Companies Need to Think Like Big Pharma When Buying Equipment
When small nutraceutical companies need to increase production, their owners tend to ask, “What’s the cheapest way to increase production?” Due to cash flow, financing access, uncertainty about the company’s long-term viability, or other issues, the thought process often focuses on meeting the immediate demand – on getting orders out the door – at the lowest cost possible. The initial cost of new (or used) equipment often frames the criteria when investigating solutions.
The big pharmaceutical companies that run the world don’t ask about the cheapest anything. The engineers and other managers at our pharmaceutical company customers ask, “What’s the best way to increase production?” Or, “What’s the best way to transfer powders from storage into the process?”
When investigating an equipment purchase, their criteria considers cost, of course, but it’s usually not at the top of the list. Big pharma focuses first on achieving the desired product quality at maximum efficiency. Then they look at items like worker safety, maintenance needs, longevity, compliance with FDA regulations, and payback period, among others. When arriving at the best way to specify equipment for a given project, the best way wouldn’t be excluded based solely on cost. Sure, these industry giants enjoy access to virtually unlimited budgets that smaller, growing companies simply do not. But by focusing on initial cost, growing companies may overlook the best way and end up installing a system that only solves the problem temporarily, or only solves part of the problem while creating other problems.
A new, lowest cost belt conveying system, for example, may increase production rates versus manual bag handling yet create a bottleneck upstream due to downtime for cleaning and maintenance that actually slows overall line speed. Or, this open conveyor may expose ingredients to the plant environment and invite contamination that shows up in quality testing. Or, the powdered ingredients may contribute to fugitive dust and nuisance dust in the workplace – even low volumes of ignitable powders can invite combustible dust explosions. Sometimes the cheaper approach just doesn’t last more than a year or two, and after a series of chronic maintenance headaches, it finally needs to be scrapped – back to square one.
The best way to avoid these pitfalls is to find the best way to solve the problem for each, individual process. This may mean automation. It may mean hiring. In terms of powder transfer for pharmaceutical and nutraceutical ingredients, the best way is typically a pneumatic vacuum conveying system. This way, the ingredients are gently transferred from storage to discharge into the process within enclosed, dust-tight piping for protection from contamination and from explosions. It’s far safer and easier than manually carrying 55 lb. sacks up a mezzanine for dumping into a mixer.
By adopting the thought process of these global pharmaceutical giants, smaller, growing nutrition companies can meet demanding quality requirements at high production rates yet run a safer, more efficient, and more profitable operation.
Learn more about the best way to convey bulk materials here.