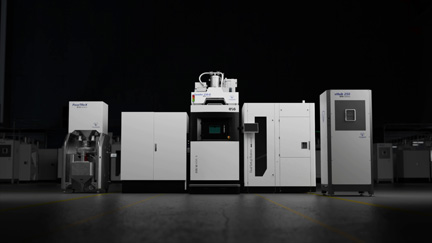
Automating Metal Powder Handling Unlocks Efficiency, Scalability
3D printing has earned attention as a highly advanced, increasingly viable process destined to transform manufacturing and push the boundaries of complex parts design. Dramatic headlines promote printing innovations involving expanded print envelopes, multi-beam laser systems, beam shaping technology, and a variety of other impressive advances, nearly all intended to boost the printer speed and allow the mass production of metal parts at scale. But while the speed of 3D printing equipment dominates headlines as the obstacle to high volume production, savvy additive manufacturers are uncovering a less visible but equally vital part of the process and unlocking the production efficiency needed to scale.
The secret is the metal powder handling process. The current state of how metal powders are transferred and managed automatically in the most advanced additive manufacturing facilities in the world is perfectly described and detailed in this new educational series, “Perfecting Powder Handling,” at the EOS Additive Manufacturing Blog here.
How to Automate Metal Powder Handling for 3D Printing
The three-part series, developed by our OEM printer partner EOS in collaboration with the Volkmann additive manufacturing team, identifies manual powder handling as a key obstacle to high volume part production. Most 3D printing companies begin operating with a single printer using small quantities of metal powders purchased in containers under 50 pounds. Workers carry the powder containers to the printer, load the powder into the printer by hand, and then manually unload and sieve excess powder. The potential exposure is unsafe for the workers and it’s a slow and cumbersome process that cannot keep pace with the demands of scale, no matter how fast the printers become.
To speed the process and protect workers, we’ve made automating every step of the metal powder handling process smooth and easy. Our closed loop bulk material handling systems automatically transfer the metal powders from storage to the printers by vacuum conveying through enclosed piping. Then, excess material is extracted from the build box, sieved to remove agglomerates, and stored for future reuse or transferred back to the 3D printer for immediate reuse. We can even mix the excess powder with virgin material in any ratio required and vacuum dry it to reduce moisture due to humidity before loading. When scale demands managing metallic powders measured in thousands of pounds, automation becomes essential for safe, efficient production.
Automation Improves Workflow Efficiency, Part Quality
As stated perfectly on the EOS blog, our automated powder handling solutions offer several immediate and long-term benefits to your production process. First and foremost, automation drastically reduces the amount of manual intervention needed, increasing safety, and freeing up operators to focus on higher-value tasks. This not only improves overall workflow efficiency but also minimizes human error, reducing the risk of powder contamination and enhancing part quality.
In addition, the system’s ability to maintain a closed (powder) loop process protects the metal powder from harmful environmental exposure, keeping it clean and reusable, and contributing to sustainable manufacturing practices. Available inerting of the powder storage and powder transfer (closed gas loop)
further protects sensitive metal powders and can be included as an option if needed. Automated handling also increases the machine’s productive time by streamlining the process of loading and unloading, helping you maintain a higher production rate with fewer interruptions.
As part of the cooperation agreement between EOS and Volkmann, the most advanced automated metal powder handling system ever manufactured is now available to 3D printing companies worldwide that use EOS printers. It’s called the EOS Edition line of our closed-loop, automated metal powder management system and it’s specifically engineered for seamless, easy integration with EOS metal additive manufacturing (AM) systems. These systems can accommodate nearly any production capacity at scale and can grow and expand as your 3D printing company grows and expands.
If you run a 3D printing company using EOS 3D printers and are trying to scale, then this automated metal powder handling system may be the breakthrough advance that novices overlook but you’ll recognize as truly remarkable and revolutionary.
Read the “Perfecting Powder Handling” at the EOS Additive Manufacturing Blog here.
Volkmann also produces metal powder handling systems and equipment that are compatible with 3D printers from all other printer manufacturers to automate, scale and boost efficiency in non-EOS installations.
Learn more about the Volkmann metal powder handling equipment here.