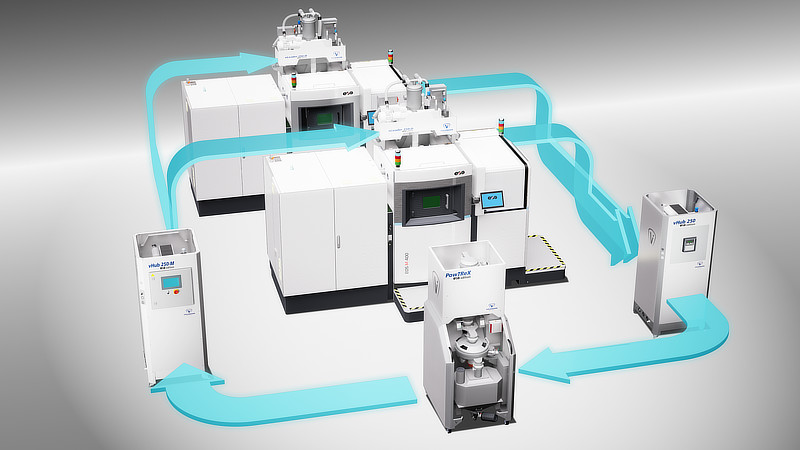
Considerations for Metal Fabricators Adding 3D Printing Services
Volkmann Engineer Offers Guidance on Metal Powder Safety, Efficiency
Bristol, PA: Metal fabricators considering investing in 3D printing equipment may be surprised to learn that expanding into additive manufacturing isn’t as simple as expanding the range of services with a new laser cutting machine, according to David Nichols, vice president of sales and marketing for metal powder conveying equipment manufacturer Volkmann USA, Bristol, PA (https://www.volkmannusa.com). Nichols offers the following considerations for metal fabricators interested in offering 3D printing services:
Additive Manufacturing Reverses Subtractive Machining
Metal additive manufacturing involves a completely different set of machinery and equipment than traditional subtractive metalworking and comes with distinct safety risks. Instead of removing material with machining and cutting, additive manufacturing starts with fine metal powders and layers them into a solid part. Since many fabricators lack experience in working with bulk powders, they may also lack an understanding of their inherent dangers.
Metal Powders: Toxic and Explosive
Metallic powders such as cobalt, tungsten, aluminum, copper, and others commonly used for 3D printing are toxic in varying degrees and milled to very fine particle sizes that must not be inhaled. These powders are also ignitable and labeled combustible by NFPA. Each step in the 3D printing process invites opportunities for powder spillage and worker exposure that need to be addressed in advance to prevent serious injury, disease and/or a catastrophic explosion.