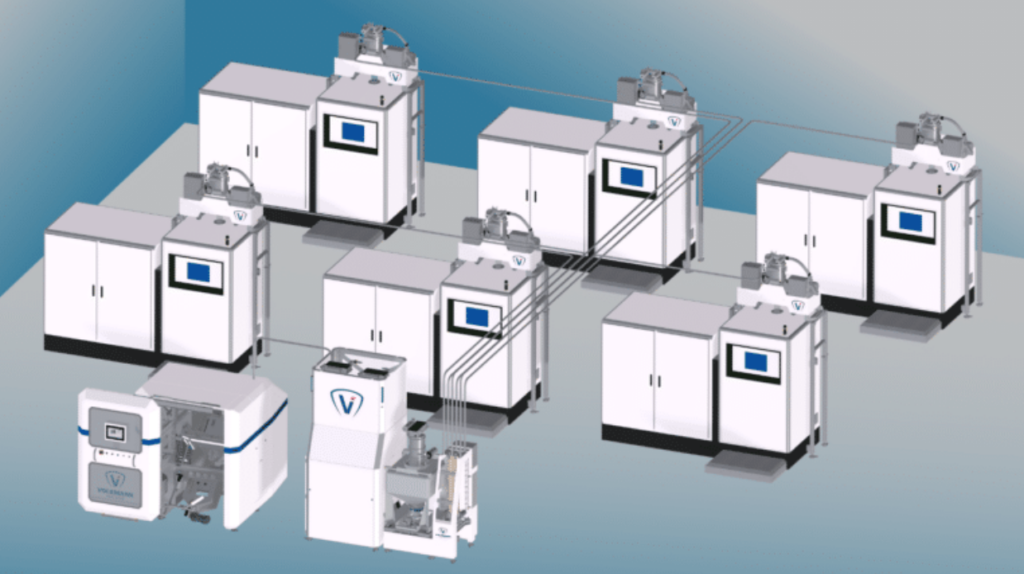
Volkmann Expands Additive Manufacturing Equipment Line, Supports Scale Up in 3D Printing
After several years in focus as the breakthrough industry waiting to break through, metal additive manufacturing commanded center stage in 2023 as the billions invested in the development of additive manufacturing technology and in 3D printing startup ventures began to yield substantial results.
At the production level, part quality, repeatability, and throughput soared while at the consumer level, “What is additive manufacturing?” ranked among the top searches.
At Volkmann, we expanded our AM product line with the introduction of a slate of automated equipment for metal powder handling, transfer, and reprocessing in 3D printing. We installed several fully integrated, closed loop systems that make the additive manufacturing process move faster and safer with greater consistency and higher volumes yet at lower operating costs. Here’s a look at how the world’s top 3D printing companies use our metallic powder equipment when they’re ready to scale up to mass production:
From our touch-screen control panel, our vLoader pneumatic vacuum conveyor automatically transfers virgin metal powder from storage and/or from an IBC set in our new vDock docking station to the 3D printer – or to several 3D printers for larger production cells. Our new vDryer vacuum drying technology automatically removes moisture until the metal powder reaches the required level of dryness. Then the new vLoader automatically purges the powder with inert gas and fills the reservoir of the printer with the dried powder.
After the 3D printing process, the build frame is automatically loaded into our new Depowdering Station where all excess metal powder is removed and collected, and the part is automatically depowdered and cleaned all in one cycle. This eliminates the need for a separate, initial, manual powder removal process by an operator at the 3D printer, and a second part cleaning cycle using different machinery. The collected powder may be transferred and screened via our PowTReX metal powder transfer and extraction system or stored in our new vHub buffer hopper before transfer to the PowTReX. This allows the metal powders to be reintroduced into the 3D printing process in a closed loop. For superior material quality, our system may also include a blending step to combine this sieved powder with virgin powder in a ratio that can be adjusted to suit each job.
And all of this happens automatically, 24/7, with little or no operator involvement.
While we’re well-known as a partner for the largest companies in the additive manufacturing of metals such as EOS, BMW, and GKN Powder Metallurgy, we’re also still a key partner to startups and other growing small manufacturers. Our new PowTReX basic, for example, packs the core powder handling functions of the PowTReX into a compact, stand-alone unit that serves a single 3D printer.
As our latest innovations demonstrate, and as our partners and customers prove every day, the future of metal 3D printing as a breakthrough additive manufacturing technology is already happening in the present.
See our automated additive manufacturing process detailed here.