vLoader, VS Conveyors
POWDER FILLING – vLoader, VS VACUUM CONVEYORS
vLoader 250: automatic filling of 3D printers with metal powder
The vLoader 250 automatically supplies a 3D printer with metal powder safely and in a fully contained manner.
The vLoader 250 consists of an integrated Volkmann pneumatic vacuum conveyor, vacuum pump, filter, and accessories mounted in a common frame installed onto or alongside the 3D printer using a support frame. The vLoader 250 is isolated from the printer by rubber isolation mounts and flexible connectors.
The vLoader 250 is compatible with any 3D printer equipped with an external powder filling connection from any manufacturer.
Powder may be transferred via fixed piping or flexible hose for distances up to 25 meters with 5 meters of vertical elevation.
The vLoader 250 can be connected to Volkmann components such as a PowTReX powder sieving station and/or vHub 250 buffer storage station, or to other components where metallic powder is stored such as a glovebox or container docking station. Manual extraction from a container is also possible.
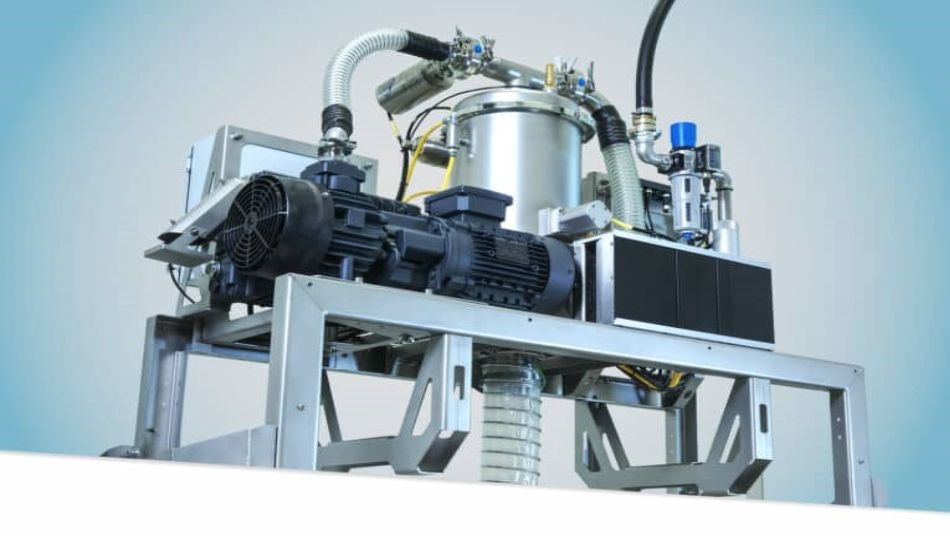
VOLKMANN vLoader 250 with integrated vDryer for powder drying
vDryer: better print quality with dried metal powder
With the optional vDryer module, the metal powder can also be dried automatically prior to discharge into the 3D printer. The improved flow properties of the dry metal powder improves the quality of the printed components.
The vDryer module dries metal powder by vacuum drying. This process is very fast and does not require additional heat input. Vacuum drying can reliably achieve a target moisture setpoint value even for batches with different moisture contents, ensuring that powder with a defined degree of moisture is always available for the subsequent printing process.
The vDryer can be integrated onto the same common support frame as the vLoader 250.
Available features and options:
- Local control or control from a centralized powder management system
- ATEX-certified documenting explosion-proof by design
- UL 508a controls
- Ability to link multiple 3D printers using multiple vLoader 250s and a common control system
- vDryer module for vacuum drying of powders prior to discharge into printer
- inert gas purging of powder batches prior to discharge into inerted printer powder reservoir
- O2 and moisture content sensing of each powder batch for traceability