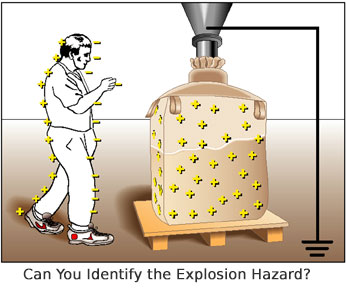
Can You Identify the Combustible Dust Hazards in this Scenario?
We received a call last year that went viral internally among our engineering team. We were rather alarmed since this call suggested that even professional engineers are confused about the dangers of combustible powders and dust and/or misinformed about how the standard operating procedures in a lot of powder processing plants could trigger a deadly explosion. Can you identify the combustible dust and other safety hazards in this process below?
A process engineer asked us about upgrading an open powder transfer system to our contained pneumatic vacuum conveying system. The existing process required workers to manually carry bulk sacks from storage up to the top of an open tank then rip open the sack, pour the powders into the tank, and discard the empty sack. The powders are manually mixed inside the tank with ethanol. Then, the mixture is discharged from the tank onto the open conveyor and transported downstream.
Let’s start with the visible safety hazards:
Requiring workers to carry 50 lb. bags across the plant and upstairs to access the tank invites risk of slips, trips, and falls. It’s also an ergonomic issue that invites back injury.
Manually ripping open the sacks, pouring out the powders, and then discarding the empty sacks typically allows some amount of fine powder to escape into the air, onto clothing, and onto the floor. Even very small amounts add up over time if cleaning is lax. These airborne dust particles not only pose a respiratory hazard but they also provide the fuel needed for a dust explosion to occur. There’s also the splash danger when clumps and chunks fall into the ethanol and the risk of contact with the discharged material on the open conveyor.
And now for the invisible safety hazards:
The ethanol in the open tank is a highly flammable solvent (even more flammable than gasoline) that emits noxious vapors into the air. Workers were breathing in these vapors on a daily basis. When these vapors mix with ambient air and combustible dust, a spark, flame or other ignition source could trigger a massive explosion. Yet there was no system for venting, removing, or otherwise safely managing the vapors in place. Their facility would’ve been classified as a gas and dust EX zone by ATEX, and the material discharged into an explosive atmosphere that would have been classified as ATEX Zone 0 or 1 (Class I Div 1).
When dry powders are poured out of sacks or bags, the sliding action often causes the particulates to separate. This creates an electrostatic charge. At the same time, a charge also develops on the sack or bag. Since the human body conducts electrical charges, a worker shuffling his or her feet while emptying the sack amid a cloud of dust could cause an electrical discharge and trigger an explosive event. This can also happen if charged dust particles on a worker’s hands or clothing come in contact with the charged bag or equipment, and bang!
This company was lucky to avoid any serious incidents but you can see why we were so alarmed. We have to keep our recommended solution confidential but for a basic idea, learn more about pneumatic vacuum conveyors.